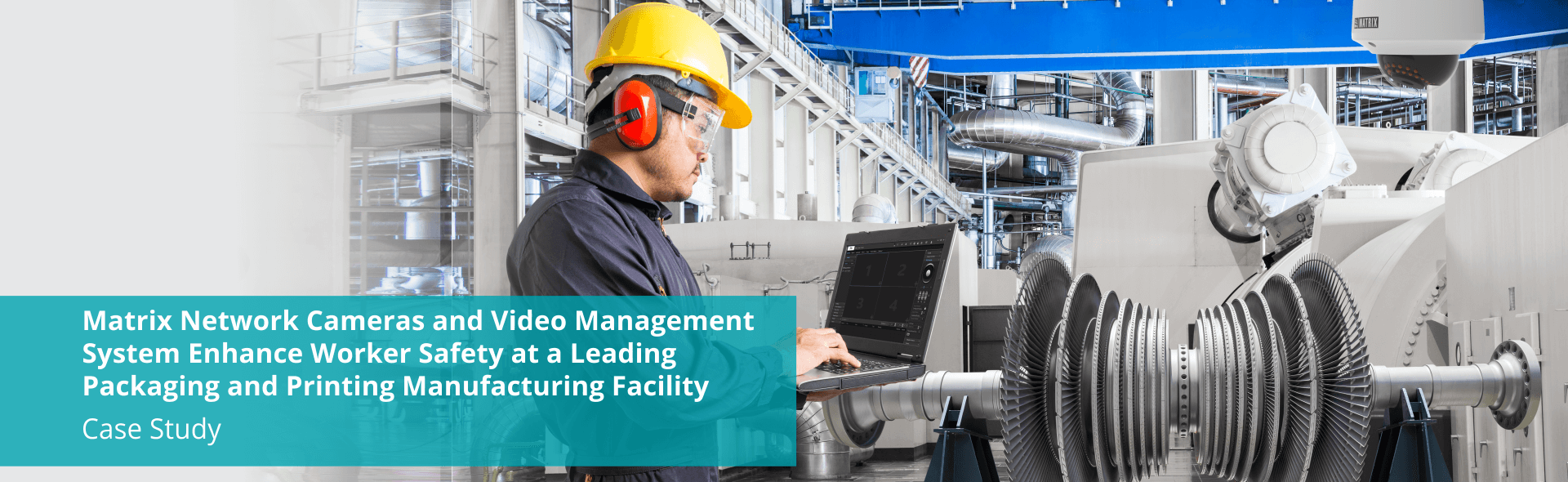
One of the leading players in the global packaging ecosystem, this manufacturing facility transforms over 100,000 tonnes of paper, paperboard, and laminates annually into diverse, high-value packaging solutions. Established in 1925, it caters to industries such as food and beverage, personal care, and consumer goods, with a robust presence across India and select global markets. Recognized for operational excellence and innovation, the business holds numerous prestigious awards and certifications. With a strong focus on customer delight and sustainable packaging, it partners with major brands like P&G, Nestle, and Unilever.
Without a video surveillance system in place, the company faced recurring security breaches and unauthorized access to its manufacturing units, which raised significant concerns for employee safety and the protection of assets. Instances of product mishandling and operational inefficiencies went unnoticed, underscoring the critical need for a video surveillance system. To address these challenges effectively, the installation of a video surveillance system was deemed essential. Additionally, they wanted a video surveillance system which ensured uninterrupted monitoring to avoid missing crucial events.
- Security Vulnerabilities: The absence of a video surveillance system posed risks to employee safety and the protection of valuable assets such as machinery, raw materials, and finished products.
- Operational Oversight: Instances of product mishandling were not promptly detected or addressed due to the lack of a robust video surveillance system. This compromised productivity, and quality control within the manufacturing unit.
- Loss Prevention: The inability to monitor activities effectively increased the risk of inventory shrinkage, theft, or damage to goods. This not only affected financial losses but also disrupted supply chain operations and customer deliveries.
- Inaccurate Weighbridge Monitoring: Inaccurate weighbridge monitoring made it difficult to verify truck weights before and after loading, which caused fraud and serious operational issues.
- Regulatory and Compliance Risks: Without a proper video surveillance system, it was challenging for the manufacturing unit to meet stringent regulatory standards, potentially leading to regulatory penalties.
All the vehicles entering and exiting the premises were monitored with Matrix Automatic Number Plate Recognition Solution. This solution uses Matrix’s Bullet Network Cameras with Motorized Varifocal Lens to zoom in on the number plate. SATATYA SAMAS – Video Management Software then uses OCR technology to convert this captured number plate image into a digital number and store it in the database.
The loading and unloading facility was closely monitored with the help of Matrix Weighbridge Monitoring Solution. This aided in the accurate tracking of shipments, which prevented frauds.
Matrix 5MP Dome Cameras were strategically placed above production floors, assembly lines, packaging areas, and quality control stations within the manufacturing and warehouse facility. These cameras provided detailed monitoring of manufacturing processes, ensuring product quality and operational continuity with clear footage. Additionally, they were installed in administrative offices, break rooms, and training areas contributing to workplace safety.
Matrix 5MP Bullet Cameras were deployed for robust outdoor and perimeter surveillance. They monitored loading docks, outdoor storage yards, parking lots, and security checkpoints. These cameras secured critical infrastructure such as HVAC rooms and electrical rooms, ensuring the safety and integrity of vital systems.
All 100+ cameras were integrated with SATATYA SAMAS – Video Management System aiding in live view, and playback of the network cameras in the premises. The facility also opted for the CREAM (Cognitive Response Engine and Automated Monitoring) module in SATATYA SAMAS to improve employee safety. Two IVAs were configured in this case – Tripwire and Motion Detection. The Tripwire IVA could be used to monitor specific areas that had to be obstructed, while Motion Detection IVA helped in identifying accidents or unusual activities in the obstructed areas. Both IVAs worked in tandem, providing real-time alerts and video pop-up notifications.
The video surveillance system was configured in such a way that ensured uninterrupted recording. Even if the recording server failed, the recording would be pushed to the management server by the network cameras. When the recording server was functional again, the footage was again pushed to the management server.
- SATATYA SAMAS PLT (1No.)
Enterprise Video Management Software - Matrix License Dongle 200 (1No.)
USB Dongle to Run Matrix SATATYA SAMAS - SATATYA SAMAS CAM5 (24 Nos.)
License for Adding 5 Additional Cameras - SATATYA SAMAS USER3 (01No.)
3 Concurrent User Licence for Smart Client and Mobile Client - SATATYA SAMAS ANPR3 (01No.)
3 Camera Licenses for Automatic Number Plate Recognition - SATATYA SAMAS CREAM5 (01No.)
5 Camera Licenses for Automated Monitoring - SATATYA CIBR50MVL12CWP P2 (04 Nos.)
5MP IR Bullet Camera Motorized Varifocal 2.8-12mm Lens With Audio - SATATYA CIBR50FL40CWS P2 (63 Nos.)
5MP IR Bullet Camera Fixed 4mm Lens - SATATYA CIDR50FL40CWS P2 (53 Nos.)
5MP IR Dome Camera Fixed 4mm Lens
The manufacturing facility is extremely satisfied with Matrix Video Surveillance System and is now planning to rely on Matrix for its needs at additional plant locations across India.
Matrix’s Automatic Number Plate Recognition (ANPR) and Weighbridge Monitoring Solutions streamlined operations by accurately tracking vehicles entering and leaving the premises, reducing manual errors and cutting down on weighment fraud.
Employees experienced a greater sense of security with the help of CREAM in Matrix VMS, as it lowered the risk of accidents in the facility.
With regular monitoring, the video surveillance system minimized product mishandling and prevented process errors, while also protecting assets and machinery.
Matrix Network Cameras kept a constant watch over inventories, warehouses, and storage yards, making it easy to track stolen goods using surveillance footage.
Matrix VMS and the server systems ensured 24/7 recording of the facility, maintaining continuous surveillance even in critical situations, providing a reliable and secure environment.