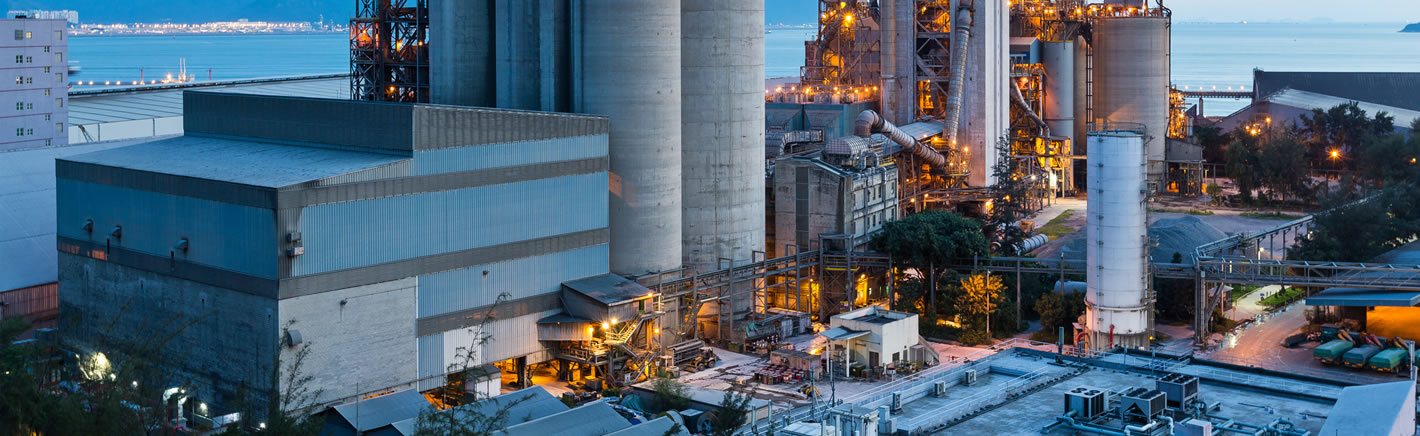
INDUSTRY : Manufacturing
CUSTOMER : A leading Cement Giant
SERVICES : Portland Cement, Portland Blast Furnace Slag Cement, Portland Pozzalana Cement and Ready Mix Concrete
LOCATION : South Gujarat, India
A leading brand of building material involved in manufacturing and marketing of Ordinary Portland Cement, Portland Blast Furnace Slag Cement, Portland Pozzalana Cement and Ready Mix Concrete (RMC) in South Gujarat integrated Matrix communication solution for the continuous and seamless communication.
Connecting its users, with different communication requirements at production plant, administration office and residential colony, dispersed over a wide area was a challenge.
Connecting its users, with different communication requirements at production plant, administration office and residential colony, dispersed over a wide area was a challenge.
- Seamless communication between Plant, Office and Residential Colony
- Efficient Call Management
- Quick Deployment
- Future-proof solution to protect investment
- Flexible Numbering Plan
- Easy to use
- Easy to configure
- Local and Prompt Service Support
- Matrix ETERNITY ME16S – 5 Numbers
- Configuration: 8 CO Lines, 4 GSM and 1400 Analog Extensions
- EON Digital Key Phones with DSS Operator Console
- Analog Phones
The end-user has one of the Composite plants in South Gujarat, India for which they sought integrated communication solution for the continuous and seamless connectivity between production plant, administration office and residential colony – all having different communication requirements.
Matrix Partner installed 5 ETERNITY ME16S – two at production plant and three at residential colony – to meet a requirement of 1400 users across the facility. All these systems are interconnected over E1 protocol offering feature transparency among users spreader over an area of 2kms. Users at distant locations are now able to reach by just dialing an extension number and also the executives in office enjoy conference bridge functionality for multiple conferences with internal and external callers.
The solution comprehensively offered enhanced internal communication as well as optimized operational productivity and call costs by intelligently routing calls to PSTN and GSM Network. Keeping all the telecommunication resources at centralized location further add to the ease of installation and maintenance to the system engineers. Matrix Systems are easy to configure and install through web-based GUI, even from the remote location. This eliminates allocation of separate technical resources for production plant and residential colony set-ups. The extensions having problem can be reprogrammed even sitting at the extension without having to go to main system and conduct reconfiguration activities – this further enhances the productivity and efficiency of system engineers and eliminates the need of commuting between user terminals and centralized system – which are spreader across the large area of 2 kms.
- On-Time Deployment
- Lowered Total Cost of Ownership
- Control over call costs
- Flexibility of call budgeting
- Freedom to Scale as and when needed
- Easy to use and manage system through web-based GUI
- Centralized Management
- User Friendly system – Minimum end user training required
- Continuous operation through Excellent Service Support
System Engineers are happy with their increased efficiency and reduced commuting across the large area due to easy and remote configuration capability of Matrix System – thus the cement giant achieved optimization of their investment and technical resources to perform better and operate more effectively by investing in Matrix System.